Capsules are a patent of the pharmaceutical and nutraceutical industries, offering a versatile and efficient means of delivering active ingredients. The capsule manufacturing process is essential for ensuring product quality, efficacy, and safety.
Types of Capsules
Capsules are primarily categorized into two types: hard gelatin capsules and soft gelatin capsules, each serving distinct purposes.
- Hard Gelatin Capsules: Comprising two rigid shells that fit together, these capsules are commonly used for encapsulating dry, powdered ingredients or pellets. They are favored for their simplicity and the protection they offer to sensitive contents.
- Soft Gelatin Capsules (Softgels): These are single-piece capsules with a more pliable, gelatin-based shell, suitable for encapsulating liquids, oils, or active ingredients dissolved in oil. Softgels provide an airtight seal, enhancing the stability of encapsulated substances.
In response to dietary restrictions and preferences, vegetarian alternatives made from materials like hydroxypropyl methylcellulose (HPMC) have been developed, offering similar functionality without animal-derived components.
Capsule Manufacturing Steps
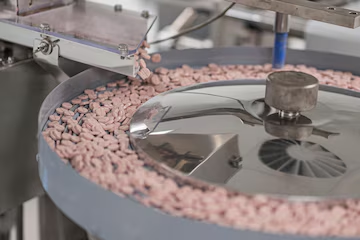
The capsule manufacturing process involves several critical stages to ensure the production of high-quality capsules.
- Raw Material Preparation: The process begins with selecting and preparing high-quality raw materials. For gelatin capsules, this involves melting and mixing gelatin with plasticizers and colorants to achieve the desired consistency and appearance. Vegetarian capsules utilize plant-based polymers, such as HPMC, processed similarly. Maintaining a controlled manufacturing environment is crucial to prevent contamination and ensure product integrity.
en.qualicaps.co.jp - Capsule Molding: In this stage, the prepared gelatin or polymer solution is molded into capsule shells. For hard capsules, pins are dipped into the solution to form the capsule halves, which are then dried and trimmed. Softgel production involves simultaneously forming the capsule and filling it with the active ingredient using rotary die machines, creating a sealed, single-piece capsule.
- Filling: Once the capsule shells are prepared, they are filled with the active pharmaceutical ingredients (APIs) and excipients. Hard capsules are filled using equipment that accurately measures and dispenses the powder or pellet formulations into the capsule bodies before sealing. Softgels are filled during the molding process, allowing for the encapsulation of liquids and semi-solids.
- Sealing and Polishing: After filling, hard capsules may undergo banding—a process of sealing the joint between the capsule halves to prevent tampering and leakage. Both hard and soft capsules are then polished to remove any external residues and enhance their visual appeal.
- Quality Control and Testing: Throughout the manufacturing process, rigorous quality control measures are implemented. This includes testing for weight variation, disintegration time, dissolution rate, and stability to ensure each batch meets predefined specifications and regulatory standards.
Advancements in Capsule Technology
The capsule manufacturing industry continually evolves, embracing innovations that enhance product performance and consumer benefits. Notable advancements include:
- Capsule-in-Capsule Delivery Systems: This technology allows for the encapsulation of one capsule within another, enabling the simultaneous delivery of multiple ingredients with different release profiles or the separation of incompatible substances.
- Enteric-Coated Capsules: Designed to withstand the acidic environment of the stomach, these capsules release their contents in the more neutral pH of the intestines, improving the bioavailability of acid-sensitive ingredients and reducing gastrointestinal side effects.
- Gelatin Innovations: To address challenges such as cross-linking and leakage in softgel capsules, manufacturers have developed specific gelatin grades that enhance capsule stability and prevent interactions between the shell and its fill material.
- Advanced Capsule Filling Equipment: Modern machinery now incorporates technologies like continuous manufacturing systems, micro-dosing capabilities for precise filling of potent APIs, and integrated quality control systems that enhance production efficiency and product consistency.
These innovations not only improve the functionality and reliability of capsules but also expand the possibilities for complex and targeted drug delivery systems.
Manufacturing Steps
The capsule manufacturing process involves several critical stages to ensure the production of high-quality capsules.
- Raw Material Preparation: The process begins with selecting and preparing high-quality raw materials. This involves melting and mixing gelatin with plasticizers and colorants for gelatin capsules to achieve the desired consistency and appearance. Vegetarian capsules utilize plant-based polymers, such as HPMC, processed similarly. Maintaining a controlled manufacturing environment prevents contamination and ensures product integrity.
- Capsule Molding: In this stage, the prepared gelatin or polymer solution is molded into capsule shells. For hard capsules, pins are dipped into the solution to form the capsule halves, which are then dried and trimmed. Softgel production involves simultaneously forming the capsule and filling it with the active ingredient using rotary die machines, creating a sealed, single-piece capsule.
- Filling: Once the capsule shells are prepared, they are filled with the active pharmaceutical ingredients (APIs) and excipients. Hard capsules are filled using equipment that accurately measures and dispenses the powder or pellet formulations into the capsule bodies before sealing. Softgels are filled during the molding process, allowing for the encapsulation of liquids and semi-solids.
- Sealing and Polishing: After filling, hard capsules may undergo banding—a process of sealing the joint between the capsule halves to prevent tampering and leakage. Both hard and soft capsules are then polished to remove any external residues and enhance their visual appeal.
- Quality Control and Testing: Throughout the manufacturing process, rigorous quality control measures are implemented. This includes testing for weight variation, disintegration time, dissolution rate, and stability to ensure each batch meets predefined specifications and regulatory standards.
Quality Assurance
Ensuring the quality of capsules is paramount, as it directly impacts their safety and efficacy. Manufacturers employ comprehensive quality assurance protocols, including:
- In-Process Controls: Continuous monitoring during production to detect and rectify deviations promptly.
- Analytical Testing: Utilizing techniques such as High-Performance Liquid Chromatography (HPLC) and Gas Chromatography (GC) to verify the identity, potency, and purity of the active ingredients.
- Stability Studies: Assessing how capsules maintain their integrity and effectiveness over time under various environmental conditions.
Adherence to Good Manufacturing Practices (GMP) and obtaining certifications like USDA Organic, Kosher, and Halal further attest to a manufacturer’s commitment to quality and consumer trust.
Advancements in Capsule Technology
The capsule manufacturing industry continually evolves, embracing innovations that enhance product performance and consumer benefits. Notable advancements include:
- Capsule-in-Capsule Delivery Systems: This technology allows for the encapsulation of one capsule within another, enabling the simultaneous delivery of multiple ingredients with different release profiles or the separation of incompatible substances.
- Enteric-Coated Capsules: Designed to withstand the acidic environment of the stomach, these capsules release their contents in the more neutral pH of the intestines, improving the bioavailability of acid-sensitive ingredients and reducing gastrointestinal side effects.
- Gelatin Innovations: To address challenges such as cross-linking and leakage in softgel capsules, manufacturers have developed specific gelatin grades that enhance capsule stability and prevent interactions between the shell and its fill material.
- Advanced Capsule Filling Equipment: Modern machinery now incorporates technologies like continuous manufacturing systems, micro-dosing capabilities for precise filling of potent APIs, and integrated quality control systems that enhance production efficiency and product consistency.
These innovations not only improve the functionality and reliability of capsules but also expand the possibilities for complex and targeted drug delivery systems.
Conclusion
Crafting capsules is a precise fusion of science and innovation, guaranteeing that each one delivers its intended benefits safely and effectively. From sourcing premium raw materials to leveraging the latest advancements, manufacturers continuously adapt to meet the evolving demands of consumers and healthcare professionals.
As technology advances, the industry is set to revolutionize capsule-based delivery systems, making treatments more sophisticated, personalized, and effective in improving patient outcomes.